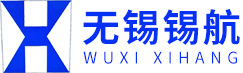
专业生产销售旋喷设备和钻具

专业生产销售旋喷设备和钻具
时间:2025-04-27
锚固钻机的锚固深度是如何精准测量与控制的?
锚固钻机的锚固深度精准控制依赖于传感器技术、机械结构设计、智能算法及行业标准的协同作用。以下是关键技术手段与实现路径的详细解析:
一、深度测量的核心技术
1. 机械计数与位移传感
拉绳编码器:
通过机械拉绳装置将钻杆位移转化为电信号,如地质深孔钻机采用的立轴拉绳传感器,精度可达 0.25% FS(满量程误差),适用于 0-2000mm 深度测量。
旋转编码器:
安装于钻杆驱动轴,通过记录钻杆旋转圈数和螺距计算深度,误差约 ±1%。例如,铁建重工 131 锚杆钻机通过编码器实现 “2 分钟钻孔 5 米” 的精准控制。
激光测距:
采用脉冲激光或相位式激光测量钻杆外露长度,精度可达 ±1mm,但受粉尘影响较大,需配合防尘罩使用。
2. 电子传感与多源融合
压力传感器:
通过监测钻杆推进力变化判断地层阻力,间接估算深度。例如,煤矿两臂锚杆机器人结合压力传感器与模糊 PID 控制,实现孔深误差≤50mm。
UWB 超宽带定位:
远程操控智能牙轮钻机采用 UWB 技术,实时监测钻头位置,精度达厘米级,适用于复杂地形的三维定位。
北斗 / GPS 定位:
大型工程中,北斗高精 RTK 定位系统与钻机姿态传感器结合,实现亚米级定位,例如张靖皋长江大桥锚固系统定位精度达 ±5mm。
3. 视觉与图像识别
工业相机:
通过视觉识别钻杆刻度或激光标线,结合图像处理算法计算深度。例如,智能锚索机器人利用视觉系统自动识别钻杆接杆位置,减少人工干预。
三维扫描:
钻机搭载 LiDAR 或结构光扫描仪,实时生成钻孔三维模型,验证深度与轨迹精度。
二、深度控制的关键机制
1. 闭环反馈系统
PID 控制:
基于传感器实时数据(如深度、压力),通过比例 - 积分 - 微分(PID)算法调整液压推力或电机转速。例如,煤矿锚杆机器人采用模糊 PID 控制,动态优化钻进速度,减少断杆风险。
自适应控制:
智能锚索机器人通过多物理场信号(如振动、扭矩)识别地层变化,自动切换钻进参数(如转速、推进力),适应 f4-f6 级硬度岩层。
2. 机械结构优化
钻杆导向与防偏斜:
采用双导轨或定心装置(如奥瑞卡 AXIS Aligner™的闭锁机构),确保钻杆垂直进给,减少轨迹偏移。
恒压推进技术:
液压系统通过压力闭环控制,维持恒定推进力,避免因地层软硬不均导致的深度误差。例如,金科 JKA-150L 钻机通过调压阀锁死推力参数,确保钻进稳定性。
3. 智能算法与数据融合
机器学习预测:
基于历史钻进数据(如地层类型、参数设置),通过神经网络模型预测最佳钻进参数,优化深度控制策略。例如,奥瑞卡 AXIS Connect™云端平台构建数字孪生系统,实时调整钻孔轨迹。
多源数据校准:
融合传感器数据(如编码器、压力、视觉),通过卡尔曼滤波算法消除噪声,提升深度测量精度。例如,地质深孔钻机系统整合拉绳传感器、转速传感器等多源数据,实现参数实时校准。
三、行业标准与工程实践
1. 精度要求
建筑工程:
混凝土基层锚栓有效锚固深度≥25mm,其他基层≥45mm,钻孔深度误差需控制在 ±50mm 以内。
桥梁工程:
大跨径悬索桥锚固系统定位精度要求 ±5mm,通过全站仪加密控制网和强制对中观测墩实现。
矿山工程:
煤矿锚杆支护孔深误差≤50mm,角度误差≤1°,通过自动校准和轨迹监测确保合规性。
2. 自动化与智能化升级
一键式操作:
铁建重工 131 锚杆钻机集成全站仪定位与自动注浆系统,实现 “一键钻孔、安装、注浆”,单根锚杆作业时间≤3 分钟。
远程监控:
准能集团远程操控智能牙轮钻机通过 5G 网络实时传输深度数据,支持云端分析与故障预警,减少人工干预。
3. 校准与维护
定期标定:
传感器需按周期(如每季度)进行实验室标定,例如奥瑞卡 AXIS Aligner™采用光纤陀螺技术,校准精度达 ±0.1°,初始化时间缩短至行业平均 60%。
自诊断系统:
钻机内置故障诊断模块,实时监测传感器状态与液压参数,例如煤矿掘进管控平台通过电流、温度分析预判设备异常。
四、典型案例与技术突破
1. 智能锚索机器人
技术亮点:
中国煤科太原研究院研发的智能锚索机器人,通过 AI 锚钻控制技术与多物理场感知,实现复杂地质条件下的自适应钻进,钻孔效率提升 2 倍以上。
应用场景:
半煤岩巷道(顶板岩石硬度 f4-f6 级),解决传统人工支护劳动强度大、效率低的问题。
2. 奥瑞卡 AXIS Aligner™系统
创新设计:
集成光纤陀螺与云端数据同步,校准精度 ±0.1°,支持钻孔轨迹的亚米级实时定位,适用于露天矿山与隧道工程。
安全提升:
机械夹持系统消除人工环绕钻杆操作风险,符合 ISO 13849 功能安全标准。
五、挑战与未来趋势
1. 当前挑战
复杂地层适应性:
软硬不均地层易导致钻杆偏斜,需结合地质雷达或随钻测井(LWD)技术实时修正轨迹。
成本与效率平衡:
高精度传感器(如光纤陀螺)成本较高,需在工程需求与经济性间优化配置。
2. 技术趋势
数字孪生与 AI 决策:
构建钻机与地层的三维数字模型,通过 AI 算法预测钻进风险,实现全流程自动化。
绿色节能:
采用电动液压系统与能量回收技术,降低能耗与碳排放,例如宇通 YTA820A 钻机的电动驱动设计。
锚固钻机的深度控制是机械、电子、算法与工程经验的综合体现。通过高精度传感器、智能算法与自动化机械结构的协同,结合行业标准与工程实践,现代锚固钻机已实现厘米级深度控制精度。未来,随着 AI、物联网与数字孪生技术的深度融合,锚固钻机将向 “自主感知 - 智能决策 - 精准执行” 的全流程智能化方向发展,进一步提升施工效率与安全性。
放眼全球,聚焦行业资讯
返回顶部
15852728887